12/15/2016: Shift Test
Below is a short video illustrating a shift test on a Sram 10-42, 11-speed cassette and shifter. This is our first prototype iteration for the Sram Drive Lever and Cable Housing Stop (i.e. pull ratio).
We're still refining performance as the set-up shown in the video has a hard time getting into the smallest ring (10t). Going forward, our work will be to ensure full range while maintaining proper cable tension and shift feel. That being said, we're really happy with the first pass! Check it out below:
10/19/2016: Fall Update
Fall has arrived in the Pacific Northwest. There's rain (lots of rain...) but also tacky dirt and plenty of loam! We've put in a lot of miles on the Long Term Test prototype and so far everything is running really well.
Some of you may wonder, how do you test a drivetrain? Our main goal is to get a large cross section of data. We test ride the derailleur in a variety of terrains and riding styes: big xc days, rough, technical descents, fire-roads, steep technical climbs, long, slow climbs, fast pump-track style descents... we even hammer road and cobblestone miles. There's a lot of variety in how people ride, so we try to represent all of them in our testing.
The derailleur currently works really well, enough that the average user probably wouldn't notice much difference with a traditional derailleur. However, there's still plenty of room for refinement. Our work is to produce and catalog any one-off lapses in performance... maybe it's a dropped chain or a ghost shift. We try to find those issues, understand them, and fix them. This is all part of the refinement process and helps ensure we put out an awesome product. Only a few photos this time from our local test rides. Check 'em out below!
-Danny
9/28/2016: Testing (aka riding bikes)
It feels awesome to finally get wheels to dirt and spin some laps on our latest derailleur! Testing has officially kicked off for our Long Term Test prototypes. So far, things are looking really good.
We plan to stay local and ride around Hood River (mostly Post Canyon) for the near future. We'll add updates here if we do some traveling. If you want to meet up, check out the derailleur, or go for a ride, hit us up at info@malcolmcomponents.com.
-Danny
9/22/2016: Frame Test Mule - Fit Check and Clear Coat
Today we got our first Kona Honzo Test Mule back from our fabricators, ADX Portland. ADX is a maker space in SE where anyone can go to use a variety of equipment. They do have everything you need to fabricate a frame, however, I am a terrible welder! Luckily ADX also has a dedicated fabrication team. I worked with Matt and Henry to bring the MC modifications to life: installing the Chainstay Bridge (thing that allows us to mount our derailleur) and sand-blasting off the original paint. After receiving the frame, we did the following:
- Perform a preliminary fit and shifting check with the frame only
- Build the bike up and do another fit and shifting check (first ride!)
- Tear it back down and prep for clear coat
- Clear coat it
- Re-build it to it's final assembled shape
Check out the pictures below!
-Danny
9/19/2016: Assembly - Long Term Test Prototypes
We're happy campers here! We just got a call from Machine Sciences; our Long Term Test Prototype parts are complete and ready for assembly. On top of that, Machine Sciences has offered to help assemble our prototypes onsite (which is good!).
Each derailleur is a pretty complex assembly. We have a number of high tolerance, moving parts plus press-fits, seals, and springs, etc. We've worked really hard to create easy-to-assemble parts, however the first assembly of a new prototype is always a learning process with unforeseen speed bumps. So, we're really stoked to have Machine Sciences adding their expertise. They're primarily an aerospace manufacturer and routinely handle complicated and critical assemblies. We bring the knowledge of the design and derailleur assembly (plus plenty of nerdy paperwork for note-taking purposes) and they bring a hefty amount of manufacturing/assembly knowledge, plus tooling and the super important "skilled assembly touch" (just the right tap of a hammer here or press there). At the end of the day, we walked away with a handful of derailleurs and lot of things learned. Plus, the prototypes turned out great!
The prototype assembly process really helps us prepare for production and higher volumes as well. As we run into little assembly problems now, we can forecast what that might look like at larger volumes. In the end, assemblies that are easy to assemble will generally be assembled correctly. So you're less likely to run into issues with out of spec parts and field failures. Which means more derailleurs out there doing their job with no fuss!
-Danny
8/25/2016: New parts!
I just picked up the first batch of parts for our Long Term Test prototypes! We received the Chainstay Bridge (CS Bridge) which is used to retrofit an existing frame so we can mount our derailleur. These specific CS Bridges are designed for a 2014 Kona Honzo, a steel hardtail with a 12 x 142mm rear end. The Honzo will act as one of our primary frame Test Mules.
After picking up parts from our machine shop, Machine Sciences in Wilsonville, OR, I took them over to our fabricator for welding. We should have our latest frame Test Mule back soon. Stay tuned for updates as more parts should be rolling in shortly.
-Danny
8/22/2016: 3D Printing
Being a small startup, we have pretty limited resources and cannot produce as many CNC machined parts as we'd like. To help bridge the gap, we lean on 3D printing. By the time we get parts machined, we've already run through multiple printed iterations. In our opinion, 3D printed parts are awesome and really valuable.
I think most people know what 3D printing is, but, I don't think the most people understand just how good it is. Production 3D printed parts are not only cool but undoubtably nice. They can be printed to high tolerances, have a bunch of available materials (including metal if you're willing to get spendy), the turnaround time is quick, and costs are a fraction of CNC machining. There are limitations of course. The parts are plastic so their mechanical properties are not as robust as metal. Also, long and/or thin parts have the tendency to warp. If you keep these limitations in mind though, you can create great prototypes that yield a lot of insight.
We've used 3D printing to validate a number of things including aesthetics, fits and clearances (think crank/heel clearance and wheel/spoke clearance), and have even used them to validate shift performance to an extent. I have included some photos below... check 'em out!
-Danny
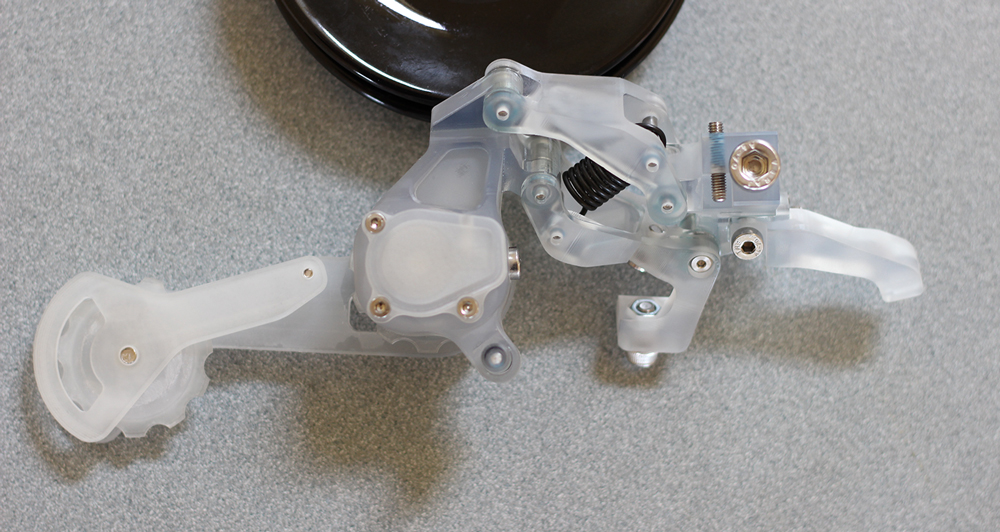
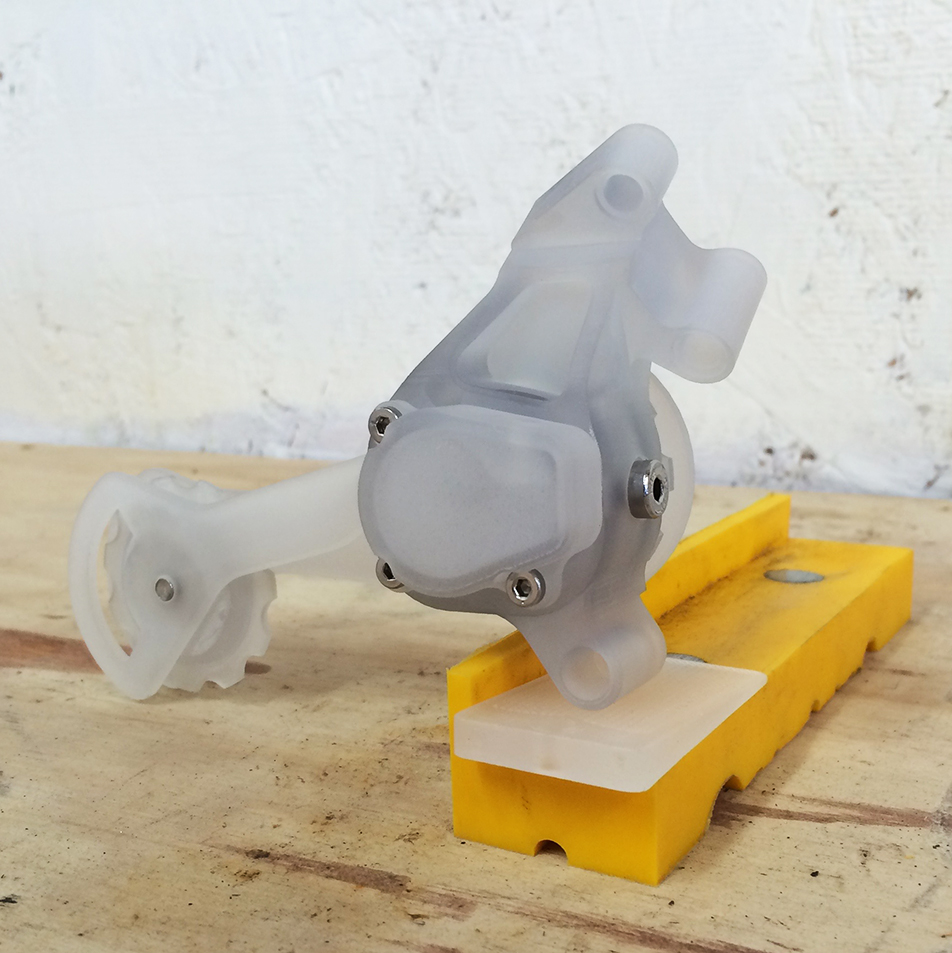
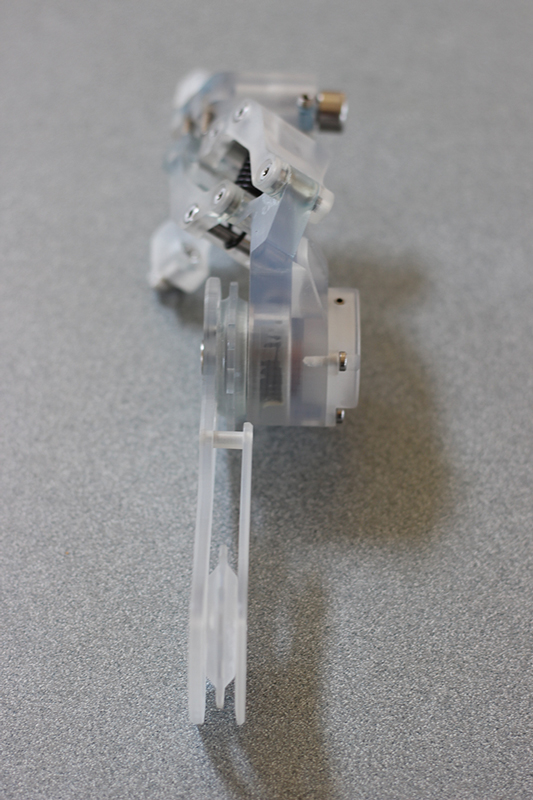
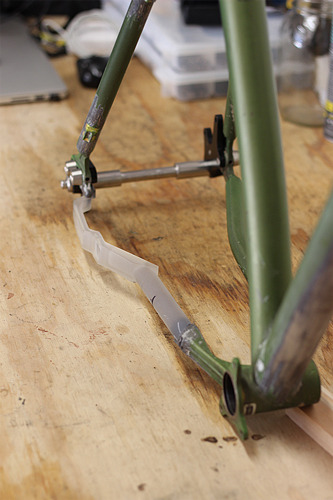
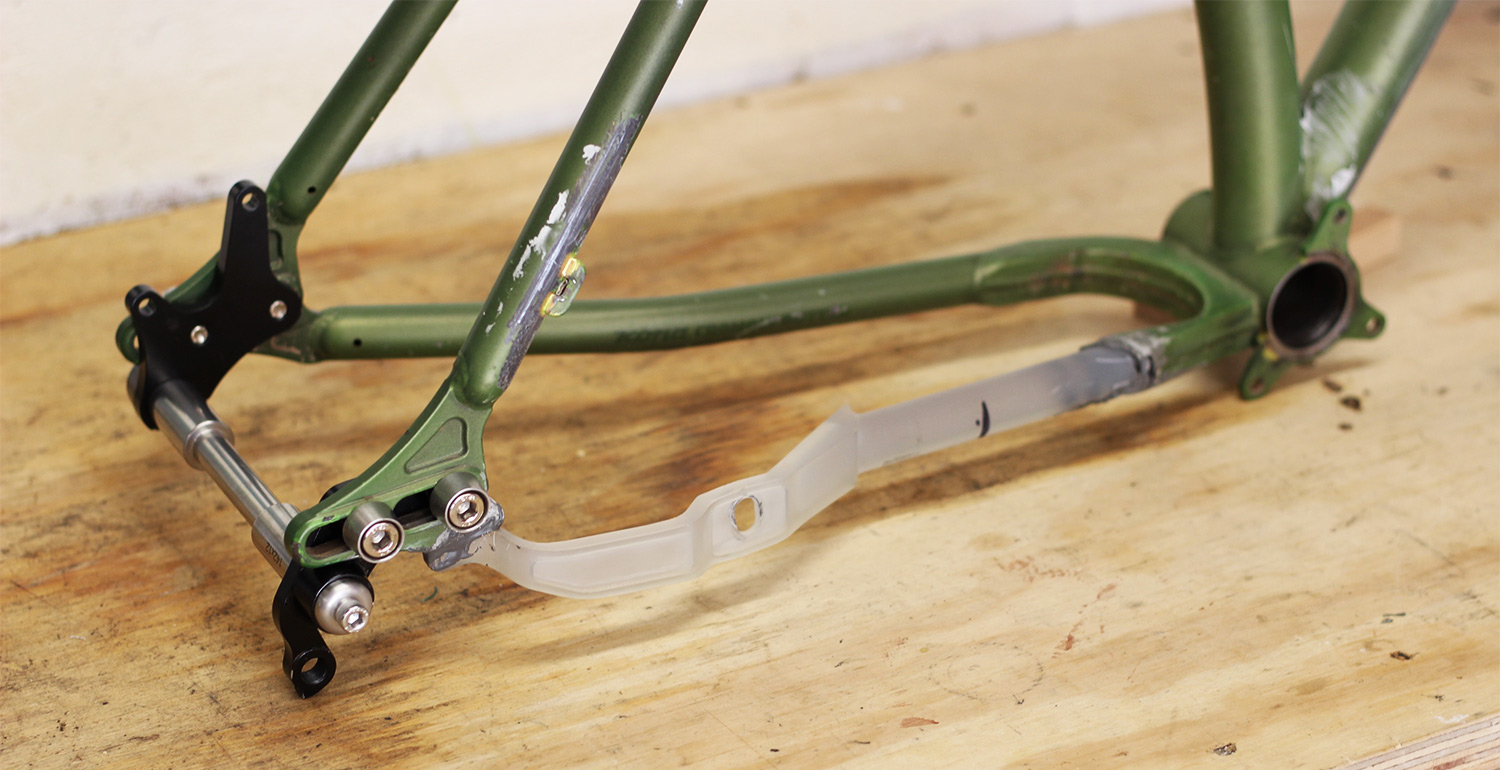
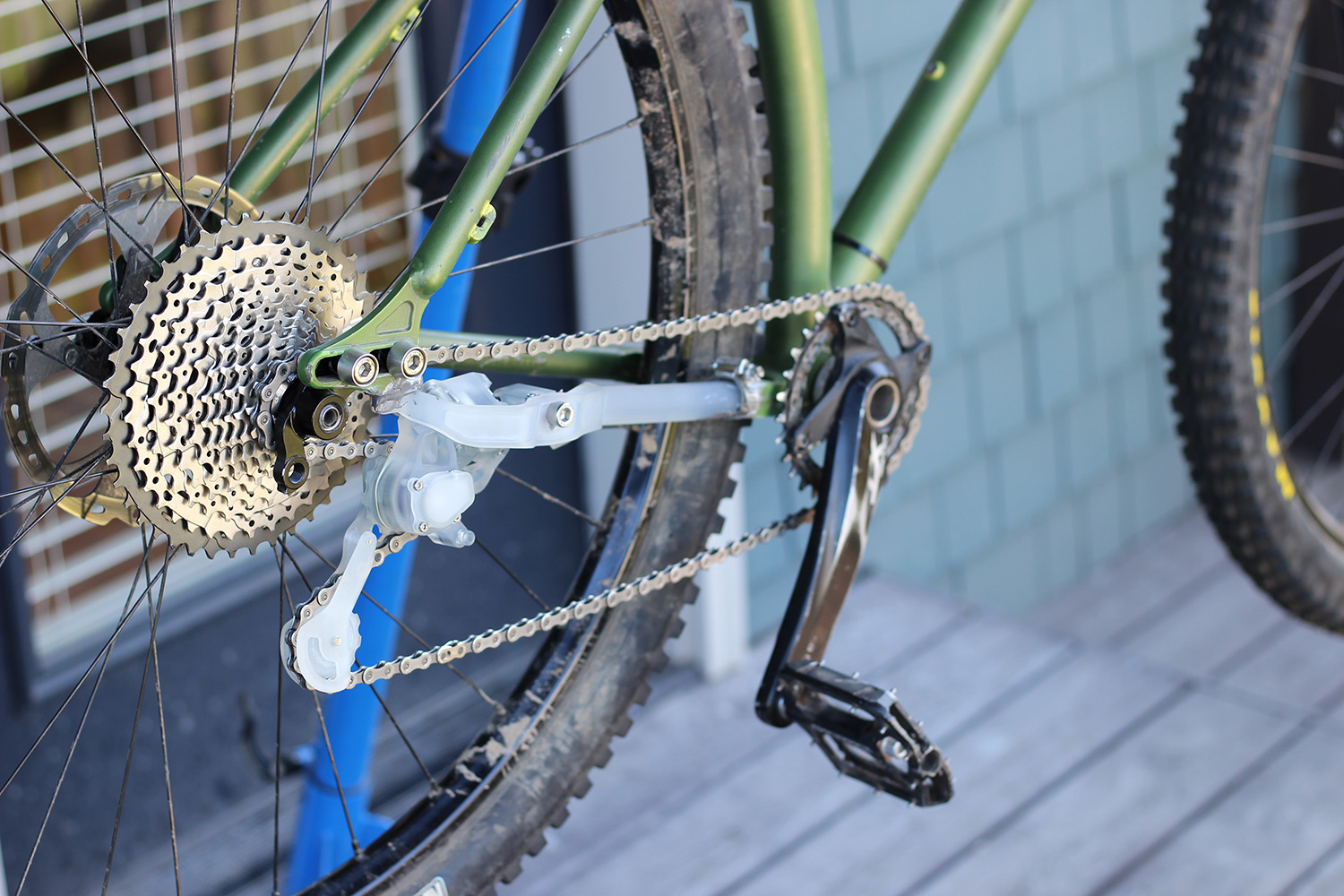